Экскурсия по Костромской ГРЭС
Костромская ГРЭС — гордость российской энергетики, одна из крупнейших тепловых электростанций Европы, имеющая федеральное значение и вырабатывающая ежегодно 3% всей получаемой в стране электроэнергии.
Сегодня я покажу фотографии с самой станции, энергоблок «миллионник», внутренности котла, а также расскажу про инновационное предприятие по ремонту и восстановлению электроэнергетического оборудования.
Станция находится в городе Волгореченске, возникшем в шестидесятые годы при её строительстве. Со своим живописным, но простеньким названием советский городок энергетиков выделяется на фоне старинной русской топонимики Костромской земли — среди таких городов, как Буй, Кологрив, Нерехта, Нея, Солигалич, Чухлома, Шарья и другие.
3-я дымовая труба Костромской ГРЭС (справа на фото) высотой 320 метров является одним из самых высоких промышленных объектов в России и 23-й по высоте трубой в мире.
В шестидесятые годы специальная комиссия изучила множество площадок от Горького до Рыбинска для строительства крупной электростанции, которая «запитала» бы сразу несколько регионов Центральной России, и только с пятнадцатого раза нашла идеальное место — устье реки Шачи при её впадении в Волгу. На выбор повлияли три основных фактора: дефицит энергетической мощности в близлежащих районах, богатые водные ресурсы и удобная транспортная инфраструктура.
С июня 1969 года по июнь 1973 года были построены 8 энергоблоков мощностью по 300 МВт. А в 1975 году началось строительство крупнейшего в мире энергоблока на 1200 МВт. Собственно он и запечатлен на фотографии.
Котлотурбинный цех № 2. Энергоблок стал уникальным во всех отношениях: по мощности, по габаритам конструкций, по характеристикам некоторых сплавов, созданных специально для него.
В 1980 году 31 декабря «миллионник» был сдан в эксплуатацию и стал самым экономичным энергоблоком станции. Общая мощность Костромской ГРЭС достигла 3600 МВт. Для примера, Саяно-Шушенская ГЭС, крупнейшая гидроэлектростанция России, выдает 6400 МВт.
Турбина длиной 72 метра состоит из пяти состыкованных цилиндров и вращается со скоростью 3000 оборотов в минуту.
Подшипник турбины блока № 9. Лопатки турбины такой длины, что их верхние части, вращаясь, бегают по окружности почти вдвое быстрее скорости звука.
Подогреватели высокого давления.
На сегодняшний день на станции работают порядка одной тысячи человек.
Котел, подвешенный на семи могучих балках на высоте 25-этажного дома, способен вырабатывать почти 4000 тонн пара в час.
Трубопровод и творческий привет от изолировщиков-жестянщиков.
Помещение блочного щита управления энергоблока № 9 (1200 МВт).
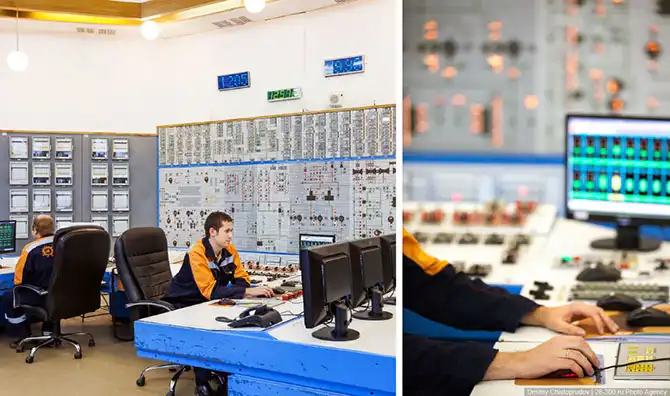
Другой корпус станции, где находятся 8 энергоблоков по 300 МВт. Несмотря на свой почтенный возраст в сорок лет, машинный зал и все оборудование выглядит чистым и ухоженным.
11 июня 1969 года в 9 часов 47 минут был зажжён факел на первом котле.
3 октября 2003 года в 0 часов 17 минут выработан юбилейный 500-миллиардный киловатт-час электроэнергии.
Коллектора котлоагрегата.
Высота котлов 300 МВт-ников достигает 42 метров. Лифты в котлотурбинном цехе имеют восемь отметок-остановок.
В буквальном смысле выражение «Фтопку» приводит именно сюда.
Топка котла с горелочными устройствами восьмого энергоблока. Температура в котле достигает 1200°С, температура пара – 545°С, давление – 255 кг/см². По бокам установлены 6 газовых горелок, почти таких же, как у нас дома, только чуть больше. Повторюсь, высота котла примерно с 12 этажей.
Весь процесс работы ТЭС в одном предложении: это электростанция, вырабатывающая электрическую энергию за счет преобразования химической энергии топлива (природного газа) в механическую энергию вращения вала электрогенератора.
А если не занудно, то смысл такой: в большой-большой котел с помощью насосов подаются газ (топливо), вода (для создания пара) и атмосферный воздух для горения.
В топке котла сгорает газ, выделяя при этом очень много теплоты. Внутренние стенки котла окутывает большая и сложная трубная система, по которой протекает вода. Вода нагревается до температуры кипения и испаряется.
А дальше получаемый пар перегревается сверх температуры кипения и с нечеловеческим давлением подаётся в паровую турбину, вращая ротор. Потенциальная энергия сжатого и нагретого до высокой температуры пара превращается в кинетическую энергию вращения ротора турбины, который приводит в движение электрогенератор. Кинетическая энергия вращения ротора генератора преобразуется в электрический ток. Все просто.
Теперь, когда я включаю на кухне свет, перед глазами за долю секунды проносится весь процесс получения электроэнергии и как результат — пык — загорается лампочка.
Центральный щит управления.
Щит управления прекрасен и непонятен.
Оперативная схема ПАА.
Дмитрий, тезка. Начальник смены электроцеха. Работает на станции уже 15 лет.
Дизайн табличек.
Капитальный ремонт паровой турбины. У любого оборудования есть определенный ресурс, после которого нужно либо проводить ремонт, либо замену.
Вот к примеру, обычные шпиндели клиновой задвижки. Слева — экземпляр после эксплуатации, а справа, внимание, не новый (как вы могли бы изначально подумать), а восстановленный! Восстановленный методом высокоскоростного газопламенного напыления.
Главным поводом поездки на ГРЭС был ввод в эксплуатацию инновационного предприятия «Интер РАО – Центр нанесения покрытий».
В центре будет производиться ремонт и восстановление электроэнергетического оборудования и агрегатов. Использование разработанных технологий позволит увеличить срок службы лопаток турбины в 2 раза, а также увеличить КПД энергоустановок.
На фотографии хорошо видно две кромки рабочей лопатки паровой турбины — изношенную и восстановленную.
Способ лазерной наплавки состоит в создании на поверхности изделий плакирующего слоя из порошкового материала с помощью лазерного луча. Высокая энергия и сконцентрированный луч лазера позволяют создавать прочные высокоплотные покрытия.
Новые технологии позволяют не только защитить лопатки паровых турбин от парокапельной эрозии, но и дают возможность полностью восстановить геометрию изношенных кромок рабочих лопаток.
Применение лазера позволяет проводить процесс восстановления поверхностей дозировано с минимальным тепловым воздействием на основной материал и без предварительного подогрева, что не приводит к деформации детали.
Что радует, технология разработана российскими учеными и не имеет аналогов в мире. В центре нанесения покрытий работают наши ученые, в основном моложе 30 лет.
Объем инвестиций в представленные технологии составил около 280 млн рублей.
Такие дела.
Пожалуйста оцените статью и поделитесь своим мнением в комментариях — это очень важно для нас!