Шаг за шагом: процесс оцинковки стали на производстве
Автор Blogger37
Сегодня мы окунемся в процесс оцинковки металла на Череповецком металлургическом комбинате. Нас ждет погружение в бассейн расплавленного цинка, встреча с огромным "зеркалом" высотой в дом, взаимодействие с робот-манипулятором и заманчивая ванночка с гартцинком. Готовы ли вы к этому? Тогда отправляемся в Череповец.
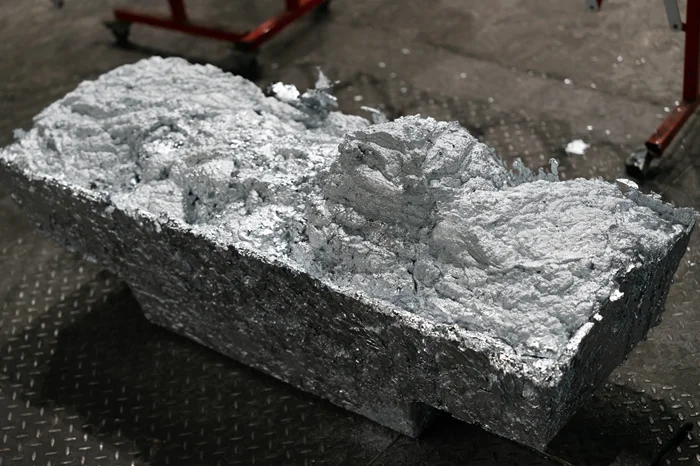
Кроме горячего цинкования существуют и другие варианты: холодное, гальваническое, термодиффузионное и газотермическое. У каждого есть свои плюсы и минусы.
Но мы сегодня «в гостях» у горячего цинкования.
Пройдем к начальному этапу агрегата.
По дороге нас встречают огромные слитки цинка.
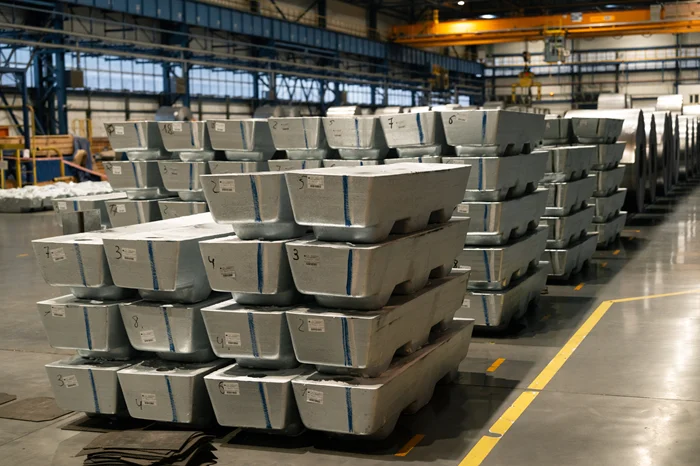
Рулоны стали поступают сюда после Стана-2000 (очень рекомендую о нем почитать у меня несколько постов назад, это нечеловечески крутая машина)
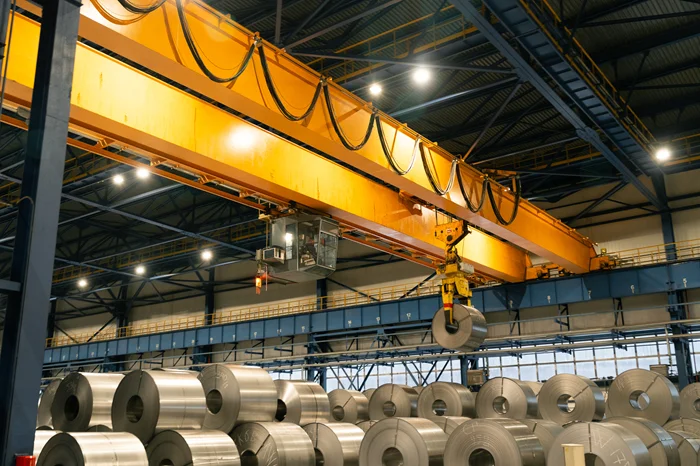
Как и на агрегате полимерных покрытий тут для непрерывности установлены два разматывателя, для непрерывной работы. Пока один рулон разматывается, второй уже устанавливается.
Максимальная масса рулонов тоже до 30 тонн
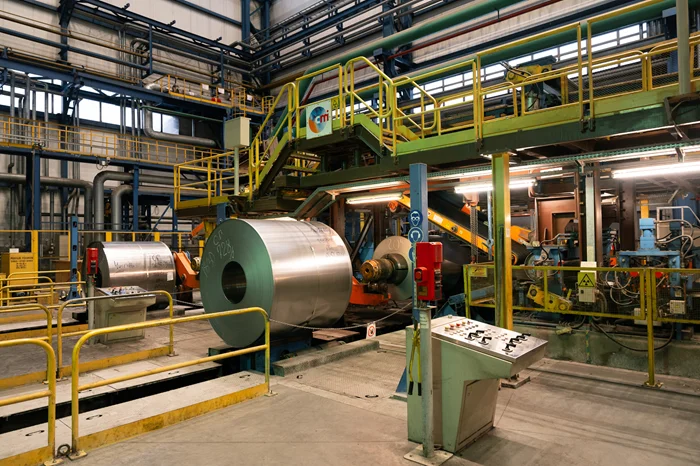
Кроме разматывателя, осуществляющего размотку рулонов, на этом участке установлена листоправильная машина (для правки переднего и заднего конца полосы с целью задачи полосы в отрезные ножницы), гильотинные ножницы (для обрезания концов полосы, имеющих дефектные участки и отклонение от требуемой толщины), сварочная машина (для сварки заднего конца предыдущего рулона и головного конца следующего рулона выпрямленным током с раздавливанием кромок стальных полос), вырубной пресс (для вырубки метки на полосе в районе сварного шва) и натяжная станция №1 — для создания заданного натяжения полосы в головной части.
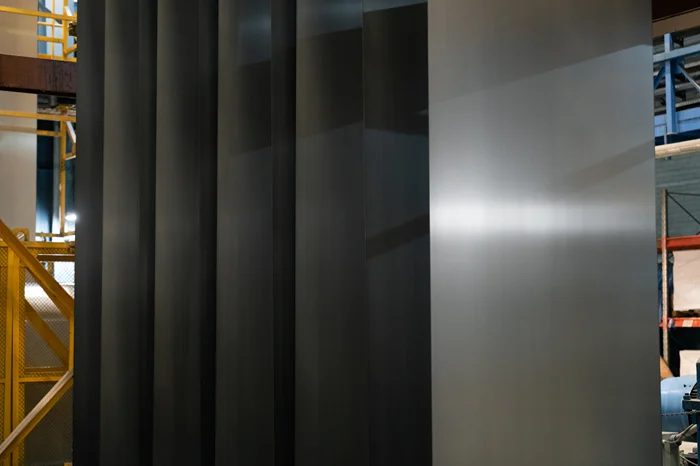
До химического узла установлено петлевое устройство №1. Оно предназначено для создания резерва полосы, чтобы обеспечить работу участка на нужной скорости, когда работа участка ввода технологической линии остановлена для смены рулона.
Полезная емкость такого накопителя 423 метра. А максимальная скорость 240 м/мин
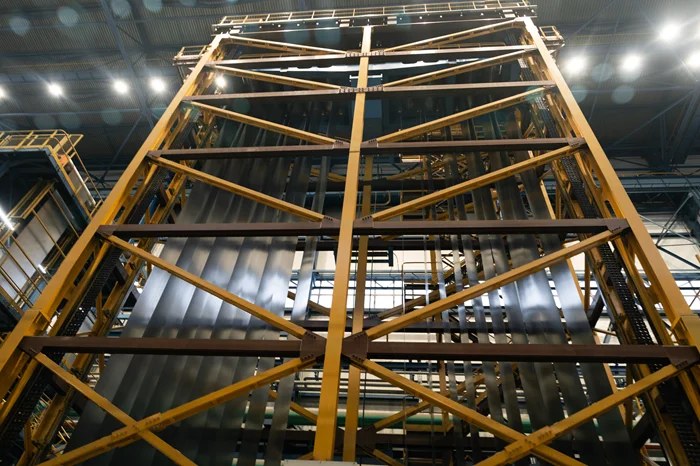
Поверхность полосы металла должна быть подготовлена соответствующим образом для цинкования.
По этой причине ее подают на химический узел. Там происходит очистка от жировых и механических загрязнений.
При помощи 6 пар щеточно-моющих роликов осуществляется механическая очистка. А химическая путем распыления щелочного раствора на полосу через форсунки (отжимные ролики потом все убирают)
Далее в секции окончательной промывки с полосы смываются все остатки раствора. Горячий воздух высушивает полосу.
Теперь полоса заходит в печь термохимической обработки. Благодаря чему повысится адгезия поверхности с жидким цинком.
В камере предварительного нагрева полоса нагревается до 250-270 градусов.
В камере безокислительного нагрева нагревается уже до 650-750 градусов.
А в камере восстановительного нагрева полоса нагревается в зависимости от назначения от 730 до 780 градусов. За этим следует камера выдержки, где поддерживается температура 730-780 градусов.
В финале полоса охлаждается до температуры расплава цинка 460 градусов в камере струйного охлаждения.
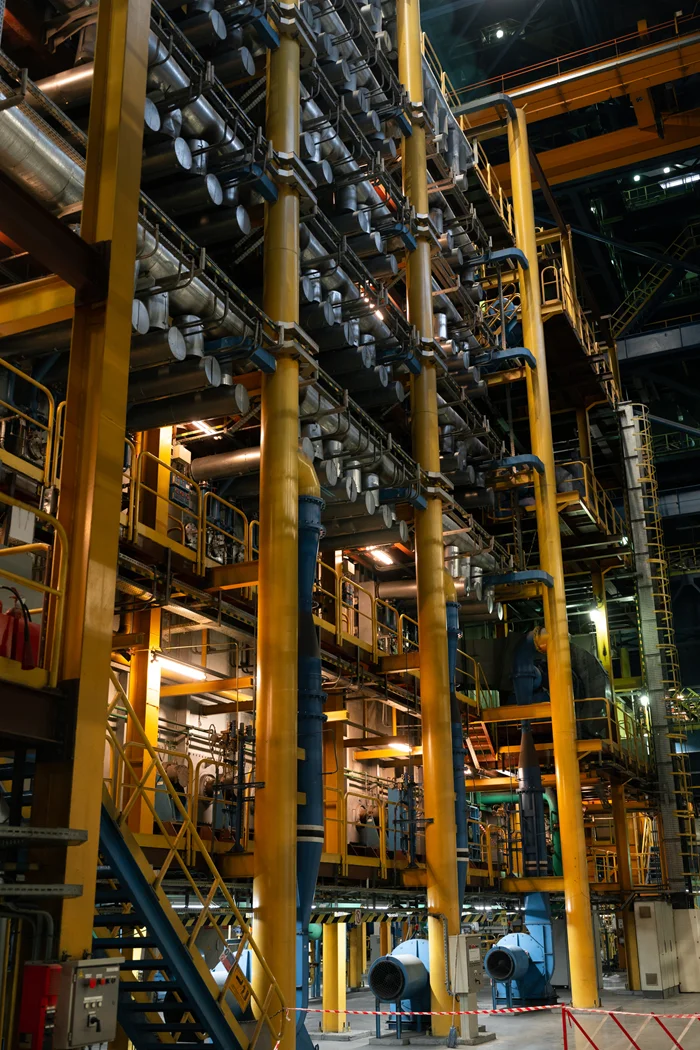
Перейдем на самое зрелищное для меня место в цеху — в участок нанесения покрытий.
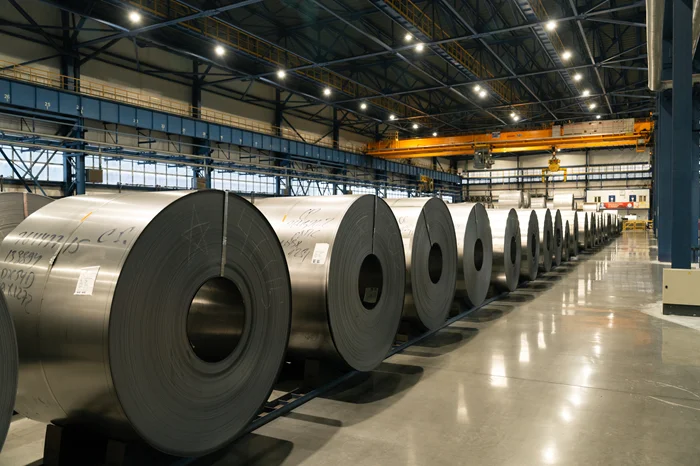
После термической обработки наша полоса, не соприкасаясь с воздухом, поступает в ванну с цинковым расплавом.
Внешне кажется, что поверхность ванны не особо большая, но в реальности ее вместимость 280 тонн расплава цинка.
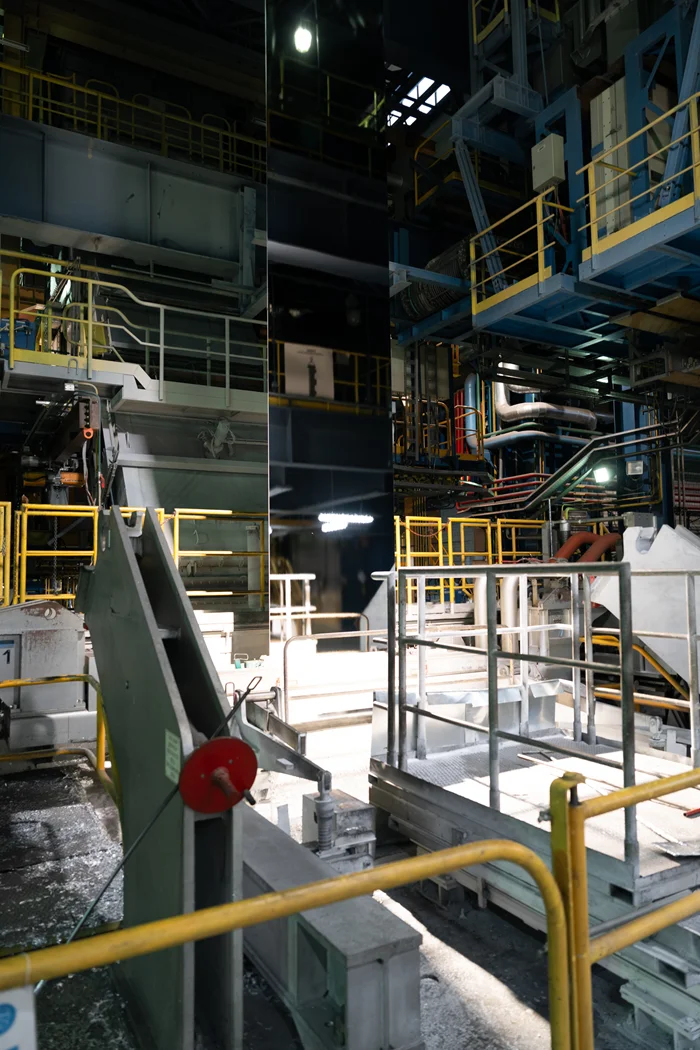
Полоса на выходе из ванны напоминает огромный зеркальный столб.
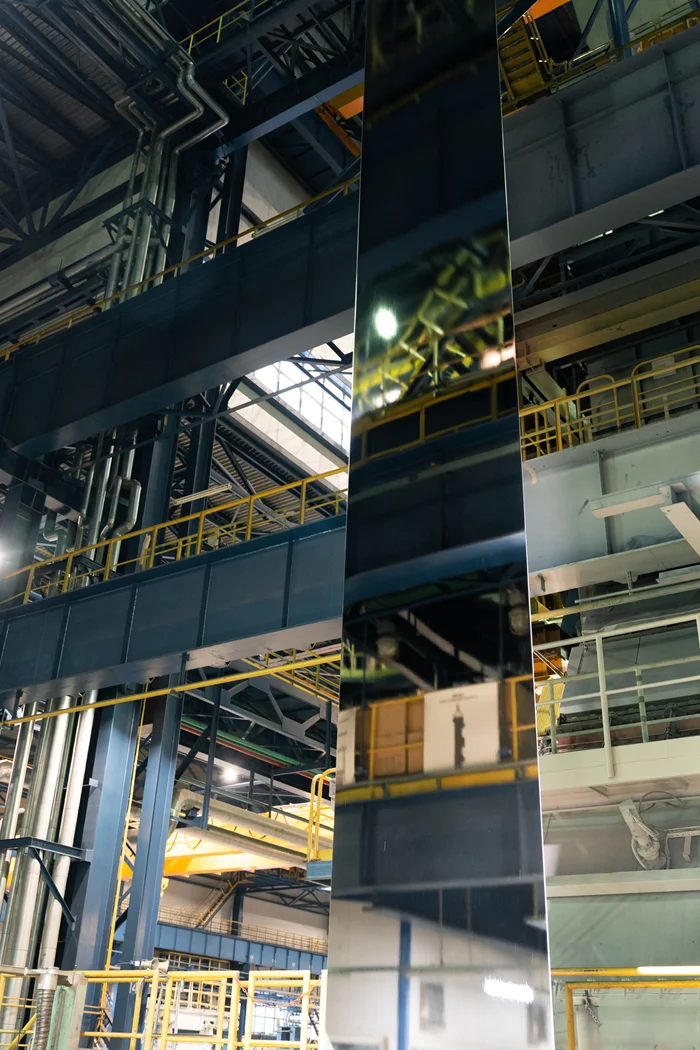
А сама поверхность расплавленного цинка так и манит к себе. Жаль ее температура в 460 градусов ограничивает все возможные контакты с ней
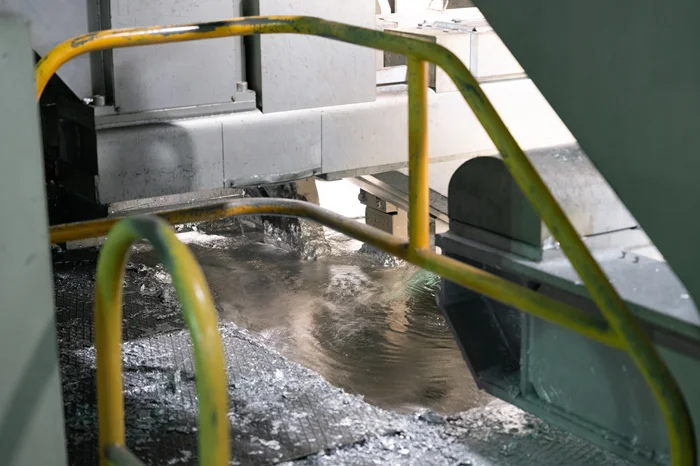
В процессе оцинковки полосы остаются отходы — изгарь (на поверхности), гартцинк и нашатырный шлак.
Изгарь и гартцинк содержат цинк. И если в первой это 55%, то во втором до 90-97%. Есть даже технологические способы извлечения оттуда цинка.
Но его же еще надо достать из этого бассейна. Пару лет назад этим занимался специально обученный человек в костюме и с титановым черпаком.
С весны 2021 года этим занимается робот-манипулятор. Своим ковшом он производит уборку с зеркала расплава. Это еще один пример, как технологии упрощают жизнь человеку.
Кстати, то корытце с гартцинком и изгарью на главной фотографии поста и есть продукт работы робота.
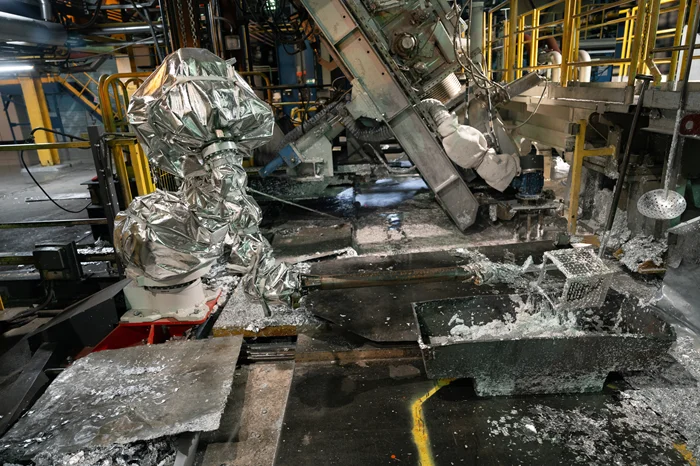
После нанесения покрытия лента поступает на 33 метровую башню охлаждения.
На начальном участке происходит охлаждение до температуры, при которой не повреждается роликами поверхность. А затем и до температуры, необходимой для водяной закалки (где она в свою очередь охлаждается от 150 до 45 градусов).
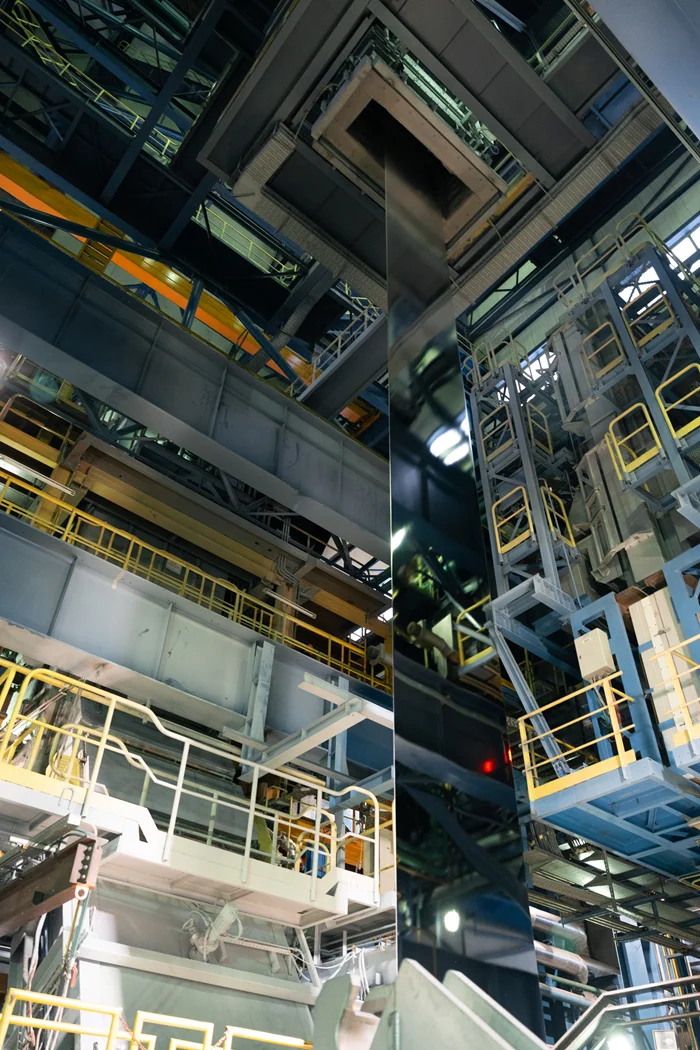
Наступает этап правильно-дрессировочного стана и изгиборастяжной машины. Это нужно для изменения внутренних натяжений металла.
После всех процедур на узле нанесения пассивации, на металл наносится тонкая пленка из оксидов хрома. Далее лента отправится в печь сушки.
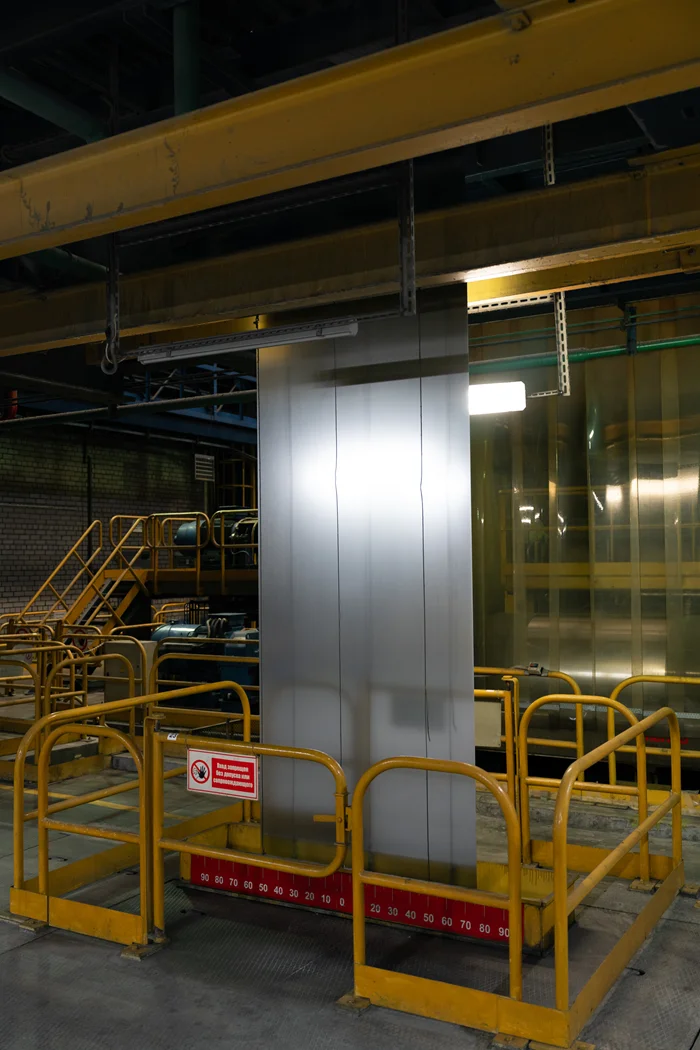
Пройдем ближе к завершающим этапам.
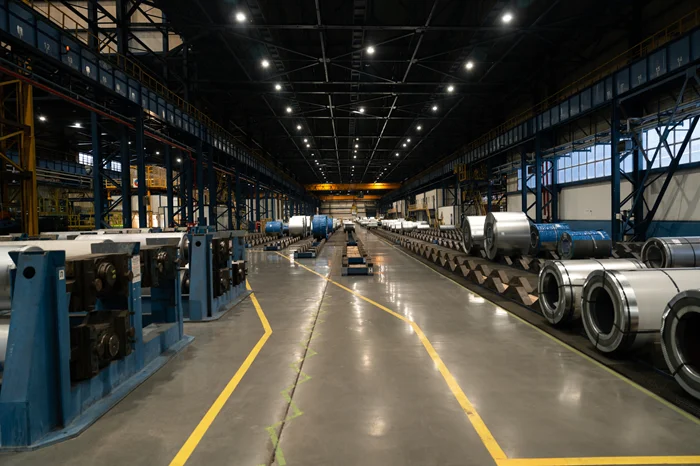
Нас встречает еще один вертикальный петлевой накопитель, обеспечивающий как и первый непрерывность и стабильность работы.
Его вместимость 280 метров.
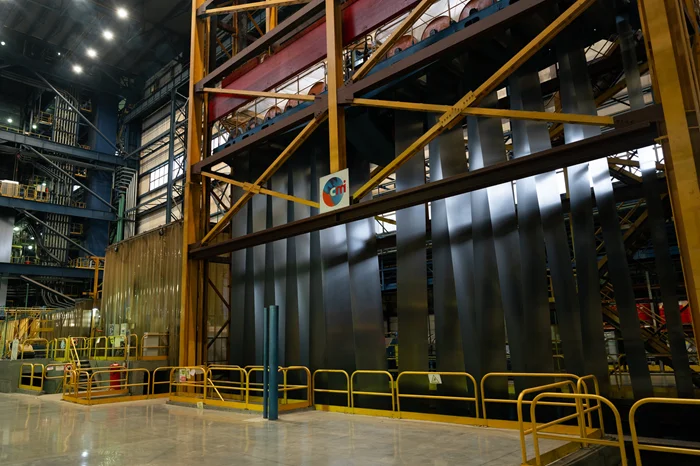
До смотки полосы в рулоны она проходит через помещение инспекции выходного участка.

Тут установлены несколько оборудованных мест контроля. На части из которых выведены данные с многочисленных датчиков системы по цифровому контролю качества.
О ней подробнее рассказывал в посте про полимеризацию и не вижу смысла дублировать информацию.
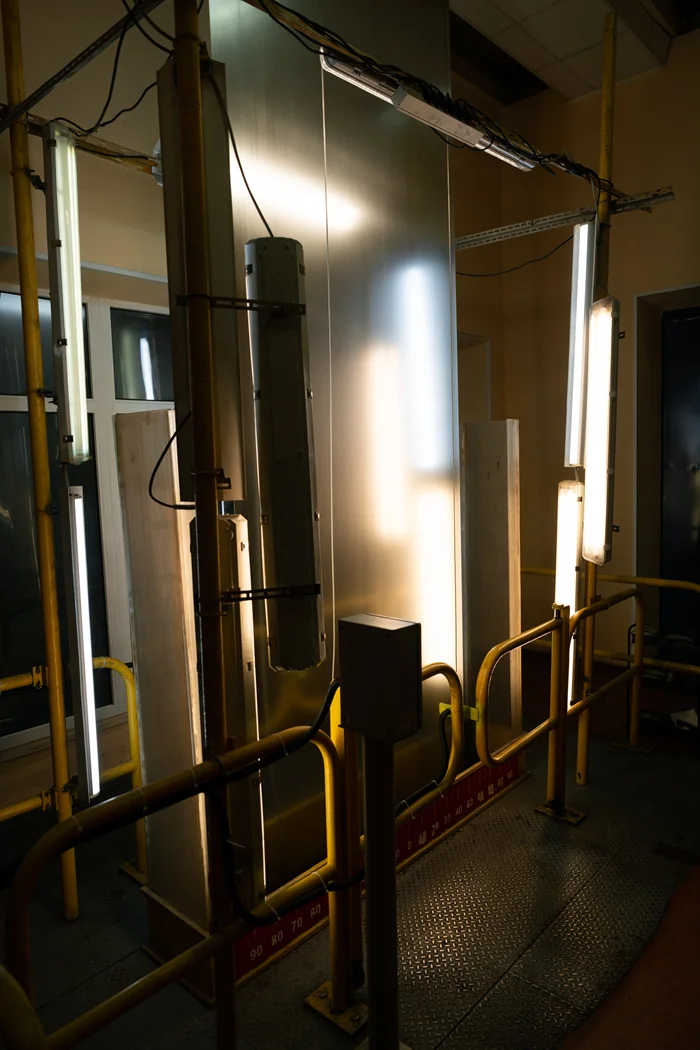
На выходе после аттестации на металл наносят защитный масляный слой на промасливающей машине.
На выходной полосе полосу обрезают при помощи барабанных ножниц. Сама смотка происходит на моталках.
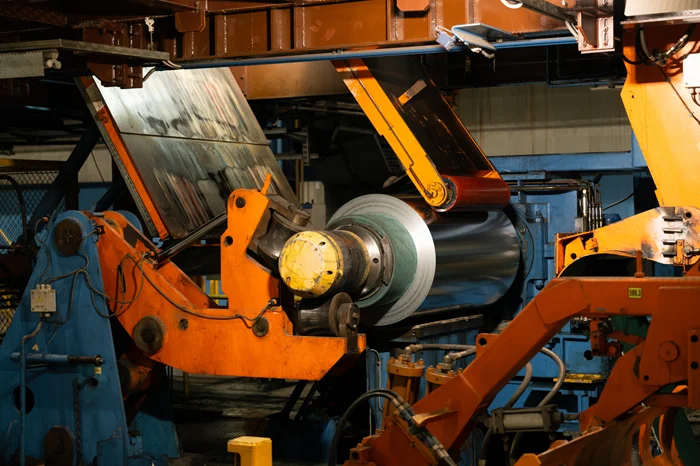
Краном рулон передается на упаковку. И тут уже в зависимости от пожеланий заказчика его упакуют в те или иные упаковочные материалы.
Впереди склад готовой продукции и доставка покупателю.
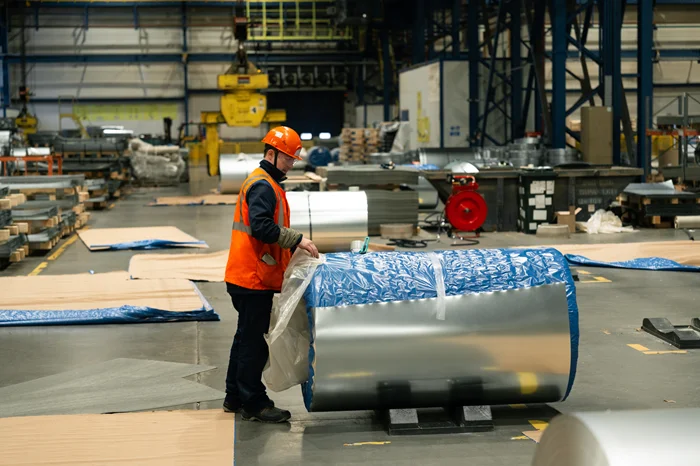
Пожалуйста оцените статью и поделитесь своим мнением в комментариях — это очень важно для нас!